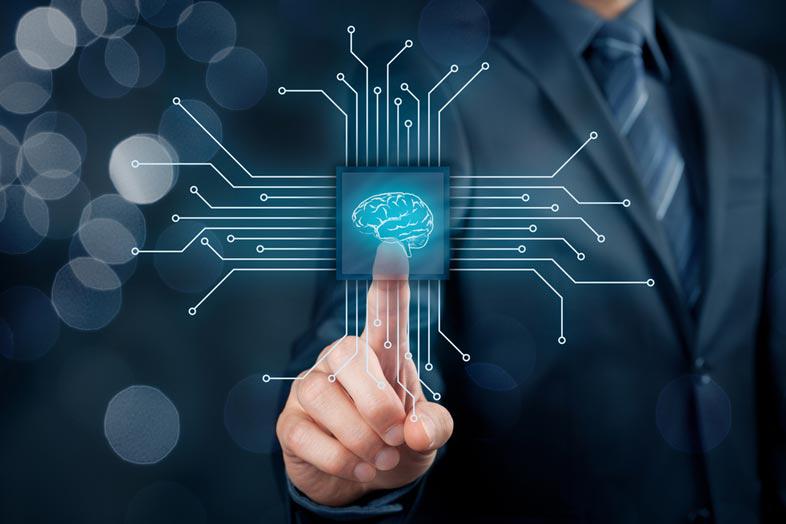
Those who work in the manufacturing industry should be well aware of the benefits that Industry 4.0 is going to bring. One of the largest benefits that Industry 4.0 is going to make possible is predictive maintenance. This article will look at how predictive maintenance and condition monitoring work and how they’re going to transform the way the world thinks about maintenance.
What is Predictive Maintenance?
Maintenance of machinery can be very expensive, and businesses can also suffer from a lack of productivity when it has to be performed. Predictive maintenance helps businesses avoid wasted time and prevent costly breakdowns at the same time, and it’s able to do this thanks to a number of factors.
Essentially, equipment and machinery that has several different compartments and components are monitored, and samples are taken at pre-determined intervals that are set by an OEM. Samples are sent to a quality lab and reports are generated that can show how worn parts are and what parts might need replacing as a result. Predictive maintenance in Industry 4.0 will take this a step further, with sensors inserted into a wide range of machinery and data being collected, analysed and shared using the Internet of Things (IoT).
Industry 4.0 relies heavily on the internet of things, which is essentially the interconnection of computing devices that can be found in a variety of products, including smart phones, car engines and manufacturing machinery. The interconnection between these devices and the internet allows them to send and receive important data, which is the basis of Industry 4.0 predictive maintenance.
What Is Condition Monitoring?
Condition monitoring is a term that’s used to describe the process of keeping track of a certain parameter of condition, such as vibration and temperature in machinery. This monitoring is done to identify any significant changes that may indicate that a fault is developing, allowing the problem to be caught and fixed before it causes any damage to the machinery. Condition monitoring techniques are usually used on auxiliary systems and rotating equipment, but they can also be used to monitor the condition of pumps, electric motors, compressors, presses and internal combustion engines. Condition monitoring is extremely beneficial, as it allows maintenance to be scheduled and other actions to be taken that will help companies to avoid costly damage and prevent breakdowns from occurring.
In Summary
Condition monitoring essentially keeps track of machinery and can identify issues before they become serious problems. Predictive maintenance does a very similar thing, but generally relies to a fairly large extent on humans playing a role in the process. Industry 4.0 will see predictive maintenance resemble condition monitoring much more closely, and thanks to intelligent sensor systems, the Internet of Things, edge computing, artificial intelligence, cloud services, big data analysis and machine learning, factories will become less reliant on humans. With machinery being less reliant on human input in order to remain well maintained and function optimally, factories will be able to be much more efficient and operate with minimal waste.
< Prev | Next > |
---|