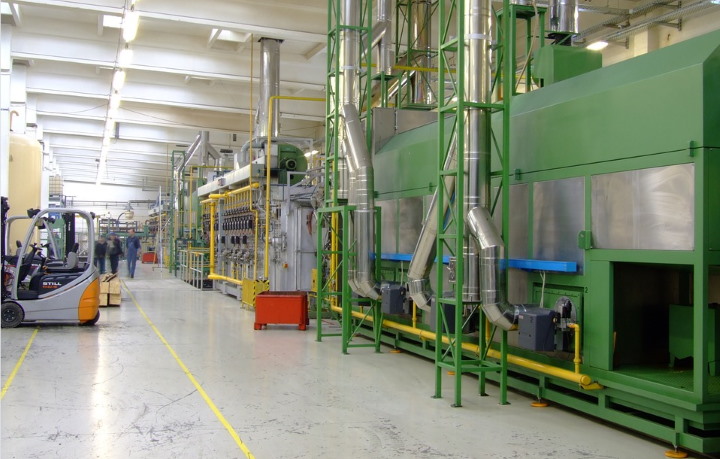
Rising sales and cutting costs has long been a tried-and-true strategy for rising earnings, so it should come as no surprise that producers are focusing on such tried-and-true fundamentals while they try to crawl out of the recent economic slowdown.
Nonetheless, facing what many see as a sluggish recovery, executives in discrete and process manufacturing industries remain largely dedicated to engaging in product innovation and developing in emerging markets. From coffee machines to rebar cutting machines the production processes need to be handled with care.
A study, in particular, gives input into how existing ERP programs are doing in terms of assisting firms in meeting their targets, what needs to be improved, and the procedures they feel have the greatest scope for change.
Although the fundamentals of success in the manufacturing sector remain constant—minimize costs, optimize reliability, and maintain your processes up to date—it is becoming extremely necessary to be able to respond to rapid changes in market and technology.
Capitalizing on Revenue Opportunities
Following one of the worst economic downturns in recent history, which struck automakers especially hard, the North American outlook for the sector is improving, though slowly.
The global environment, increased competition from developing economies, dynamic supply chains, increased regulatory standards, and volatile raw material prices force producers to track and react to a wide range of external problems while still managing their own internal competitiveness. Technology has come a long way and we must utilize that.
Manufacturing executives in North America are intensely concentrated on similar industry objectives such as increasing sales and decreasing costs. Investing in product creativity was cited as the highest revenue-creation strategy by 71% of those polled, perhaps indicating the view that after such a long slump, now is the time to leverage and take advantage of a fresh growth surge.
Meanwhile, approximately 42% of respondents said that new product introductions are a priority, while 35% said that tightening processes, distribution, and manufacturing is a priority. Manufacturers may increase sales by offering services such as installation, repair, and servicing. They will also use their information systems to find potential niche opportunities and niche technologies, as well as increase consumer collaboration through programs such as design-to-order and engineer-to-order.
Furthermore, the ability to monitor the complexities of specific SKUs is critical to maintaining the supply inventory required to provide these services.
Optimizing Operations and Processes
When suppliers struggle with the complexities of supply chains and delivery networks, the ability to customize monitoring mechanisms and measurements is becoming more necessary so that they can identify potential challenges early and change procedures until they become major problems. Production processes top the list of what executives are looking at to boost operations, as chosen by 74% of those polled. Just marginally fewer than half—42 percent—claim they are looking for opportunities to simplify the supply chain, although just 28 percent suggest they are looking to reduce the amount of vendors they work with.
ERP programs are almost often utilized by today's manufacturing firms for tracking and automating market performance processes, and such systems cover functional fields across the manufacturing enterprise, from controlling the consumer lifecycle to maximizing efficiency, increasing financial insight, and leveraging the supply chain and delivery networks.
Using ERP in the Enterprise
ERP has unquestionably had a major effect on banking and accounting. In reality, 59 percent of the executives polled said that is where their company gets the most value from ERP. A seventh, on the other hand, replied that ERP is critical in all facets of their company, although lesser sums send the thumbs up to ordering, quality management, production processes, and distribution, in descending order.
ERP tech has experienced considerable transformation over the last more than 20 years. While early devices were mainly acquired and utilized for financial applications, order fulfillment, sourcing, and production, today's systems are configured for wider business use.
Finding Consistency Across Diverse Applications
This is often the product of purchasing a firm with an internal ERP scheme that differs from the one used by the company doing the purchase. That may also be due to distributed decision-making and the willingness of modern business units to choose a more up-to-date structure than older business units.
The capacity to link these systems is vital for providing the information flow required to feed the advanced analytics technologies on which manufacturers depend to provide management with the expertise required to make critical business decisions.
Dealing with Complexity
Manufacturing leaders must still deal with the complexity of manufacturing processes. Addressing increased difficulty was ranked as a 3 or higher by 87 percent of respondents on a scale of 1 to 5. An ERP solution that serves the needs of manufacturers today must be able to assist the company in dealing with transition, which may take the shape of a shift in consumer tastes, interruptions in the supply chain, new rules, or new pricing-cutting rivalry.
Furthermore, an ERP approach that can scale with the company and enable it to handle dynamic supply chains is a valuable tool when coping with global market issues. When a company expands, it may sacrifice useful productivity when it adapts and refocuses, which may be disruptive to complicated systems which can require new practices and retraining workers, or more serious retooling and re-engineering.
< Prev | Next > |
---|